- Reporting
- Equipment operating time
- Switchover forms
- Material balance
- Enterprise model description
- Integration options
- Deployment options
Reporting
One of the key tasks of any enterprise is computing and reporting the performance indicators of equipment and the entire enterprise as a whole. Reports are generated daily, monthly, and quarterly. It is not uncommon to encounter a situation where a report needs to be compiled based on data from multiple systems. For example, power and pressure indicators are taken from process control systems, temperature from the telemetry system, and then the data is compared with planned values stored in the ERP system.
The reports module addresses such tasks by consolidating data into reports. A key point is that TechnoDoc is not limited to generating reports as a set of Excel files but creates a comprehensive solution for maintaining a long-term database of reporting documentation.
Each report has settings - viewing and editing permissions, a list of conditions for automatic generation (by schedule, by event, by the presence of a alert message in the process control system), the possibility of manual data entry, the history of manual corrections, template versioning, the ability to sign reports, export to Excel, PDF, email scheduling, etc.
Users create templates using the report form designer. The report designer has a visual HTML editor and allows designing layouts of any complexity.
Calculated parameters are available. If the built-in aggregation functions do not include the necessary one, it is possible to describe the calculation parameter algorithm in C#.
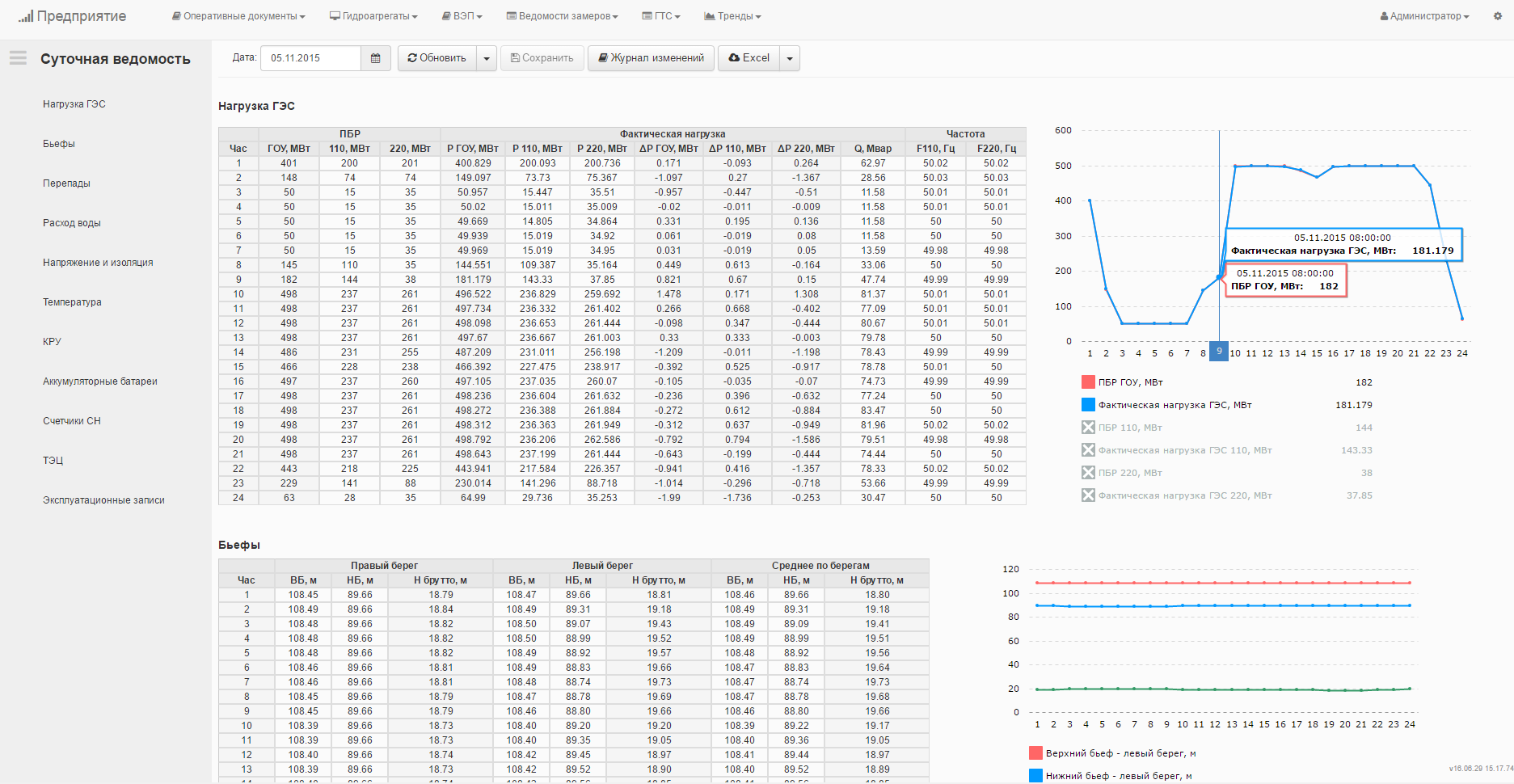
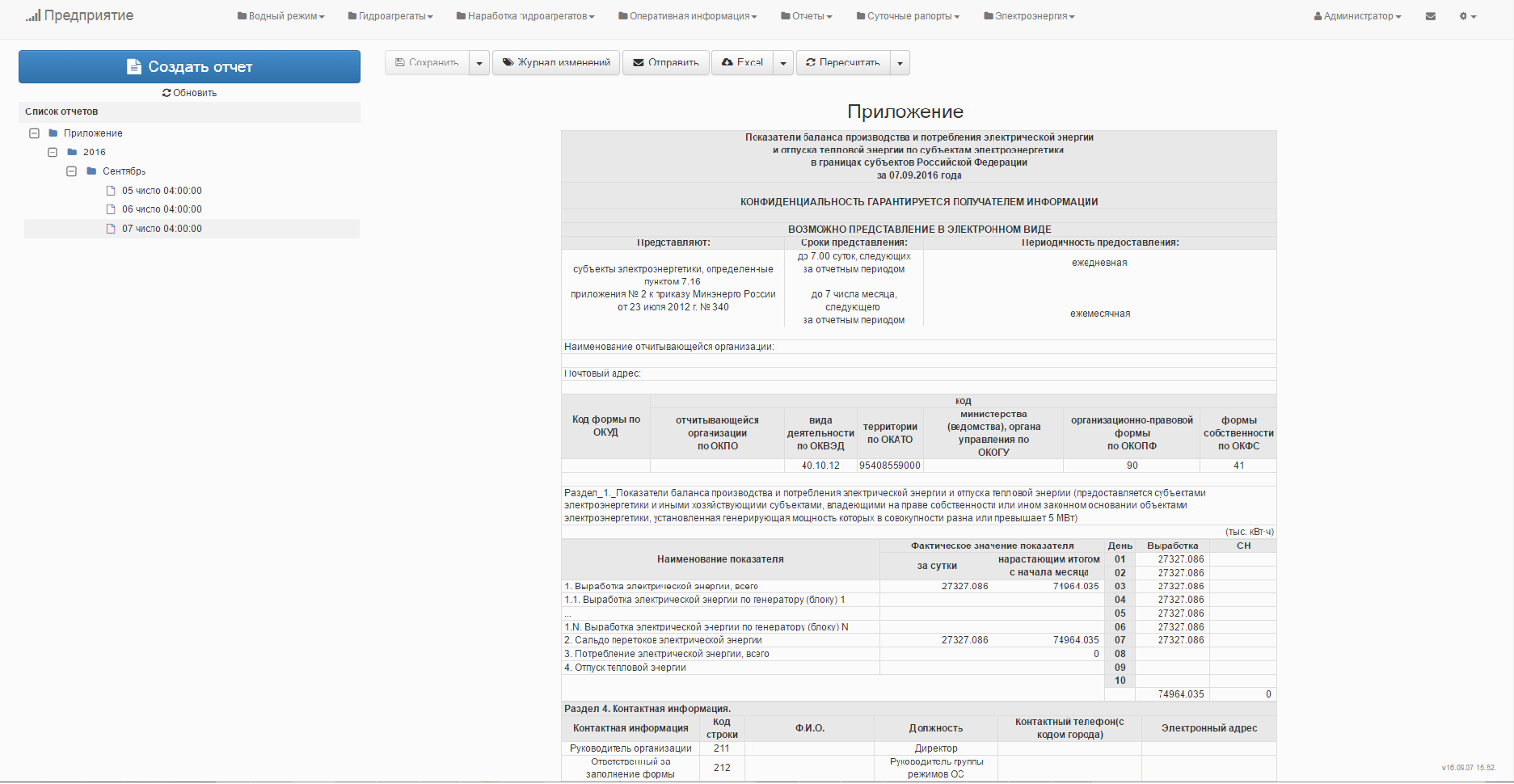
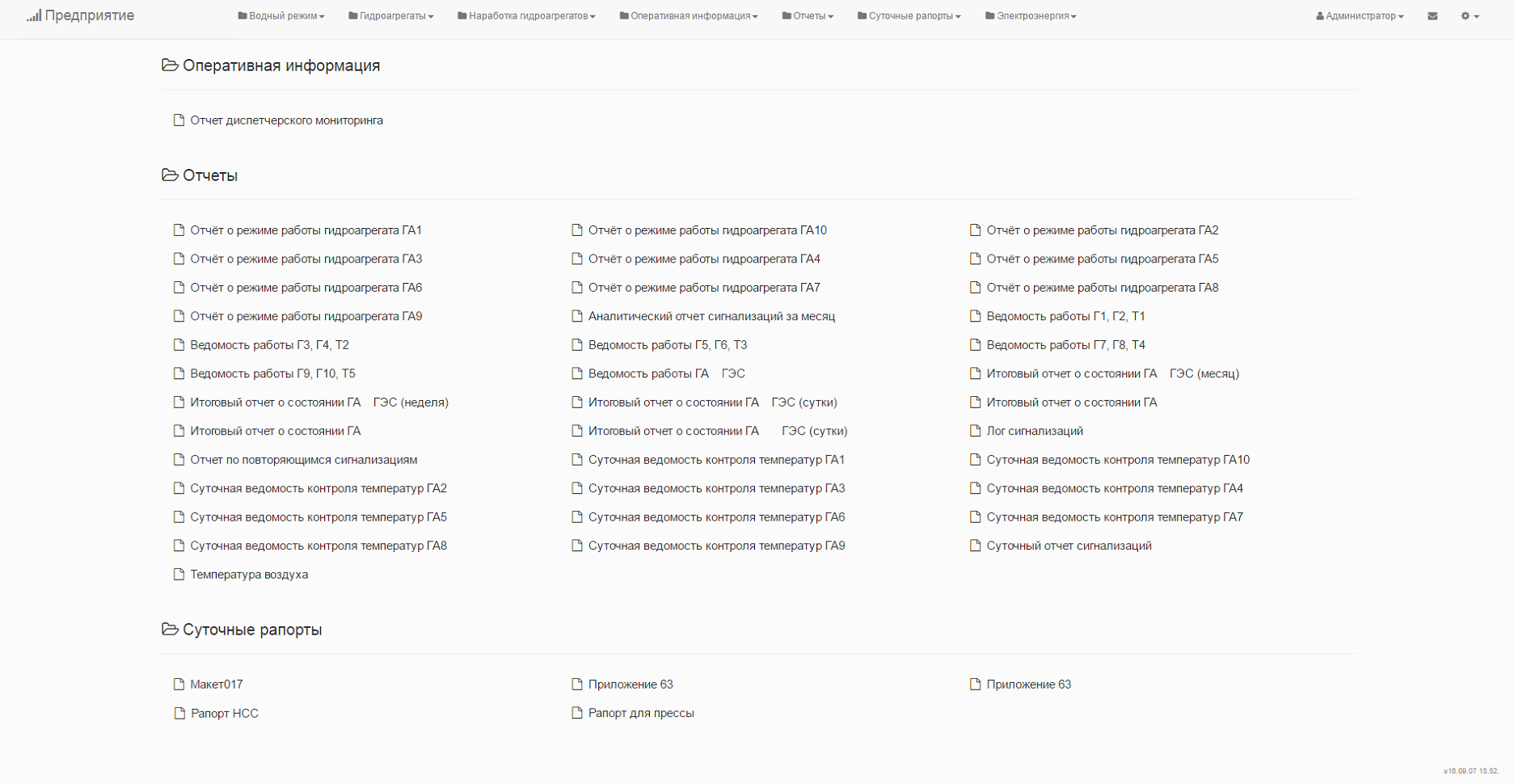
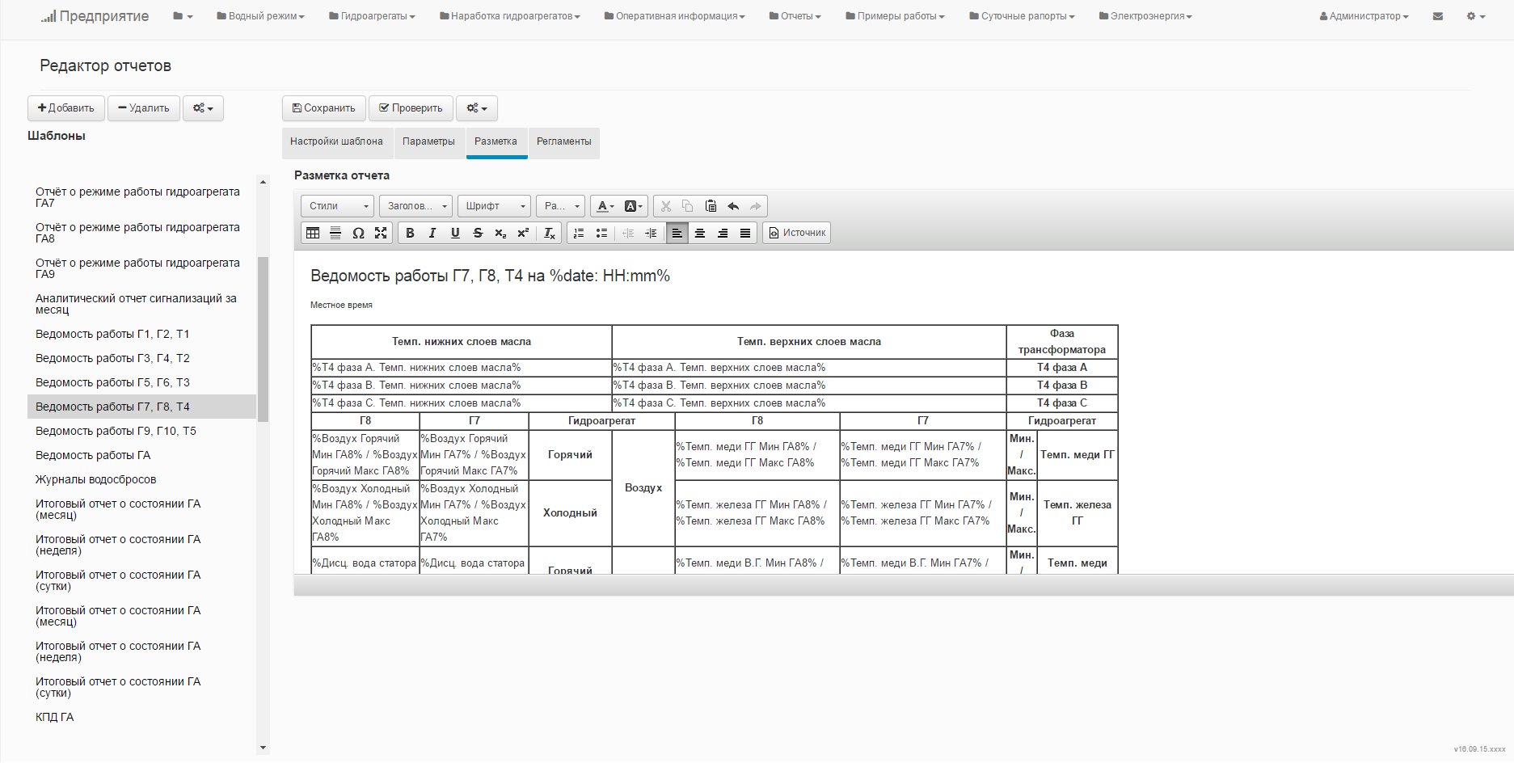
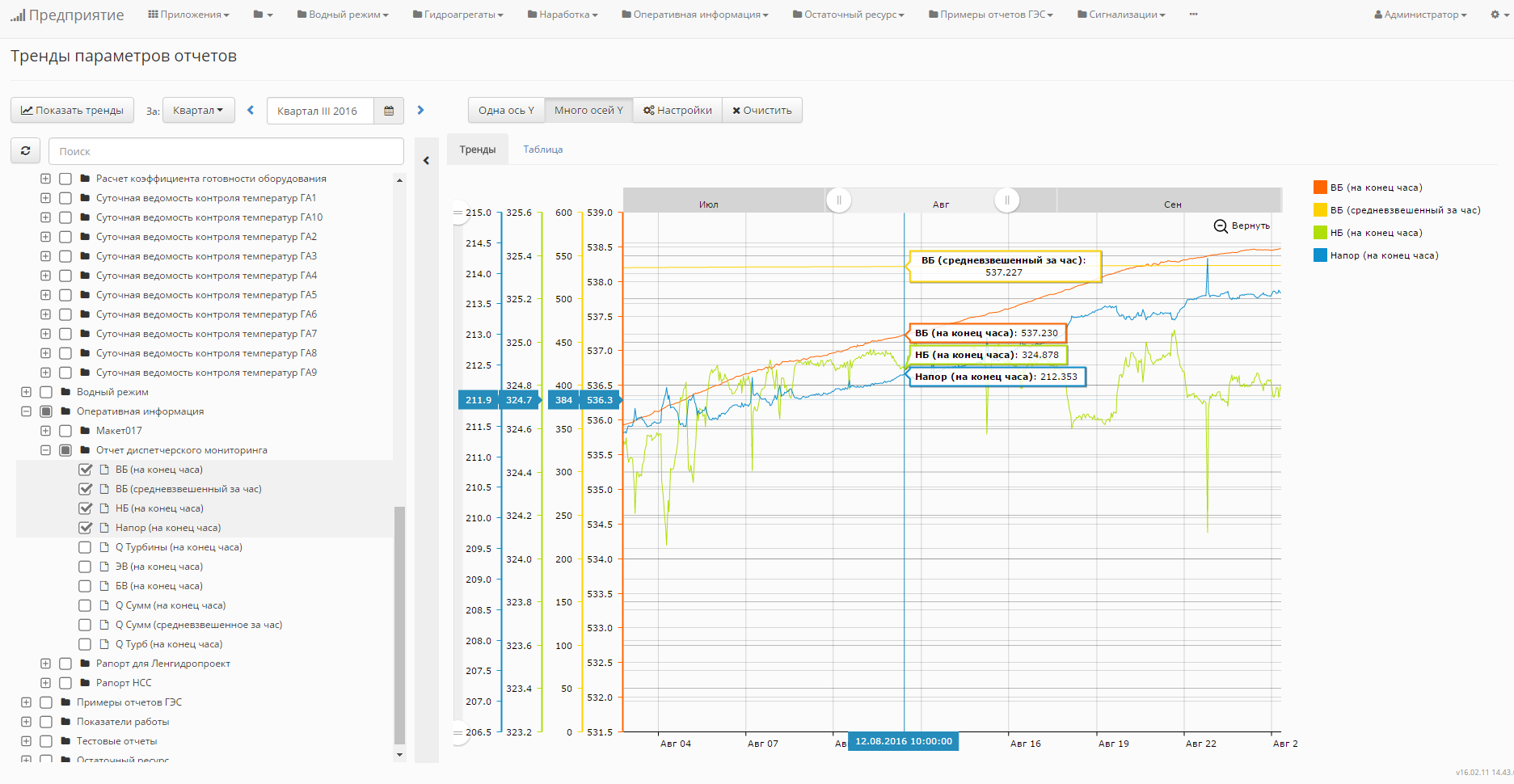
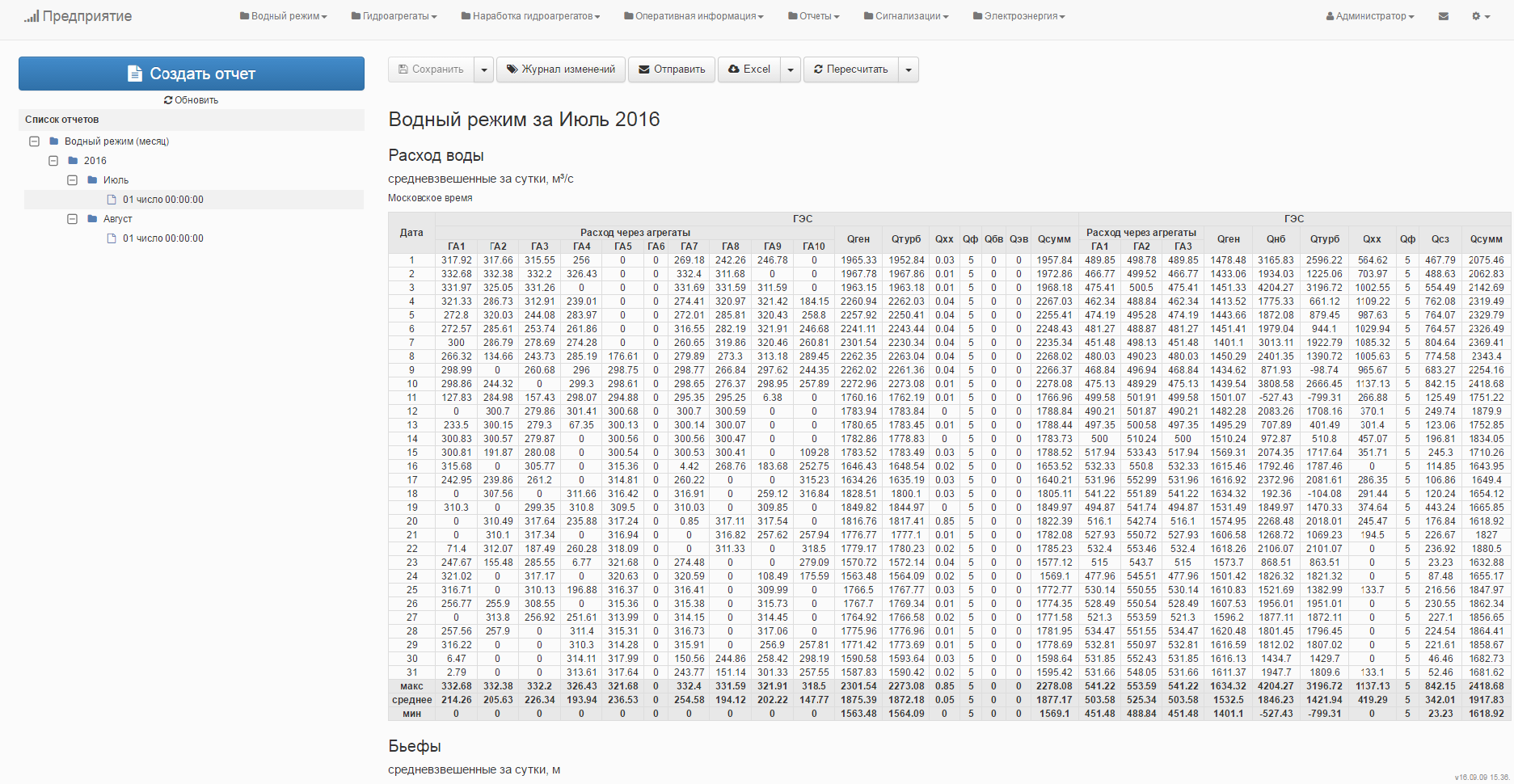
Features:
- Report form designer
- Automatic loading of parameters and messages into reports from heterogeneous systems in real-time
- Manual corrections, change logging
- Calculation of calculated parameters - formulas, aggregation, programming
- Viewing trends by parameter sets from different reports
- Report generation according to regulations by schedule and/or event
- Highlighting unreliable parameter values and dependent calculated parameters
- Export reports to PDF, Excel
- Send reports by email on schedule
- Report signing
Equipment operating time
The equipment operation module helps answer questions like 'How long has the equipment been operating in a particular mode?' and 'How many times was the equipment started and stopped?'.
To calculate the operation time, three steps need to be performed:
- Describe possible operating modes of the equipment. For example, 'Start', 'In operation', 'Stop', and 'Stopped'.
- Specify the parameters based on which the operating mode will be determined. For example, main determining parameters from the process control system can be the pressure in the pipe, the presence of flow, or the generated power, but it is also possible to determine the operating mode based on the switch state from the telemetry system or other systems.
- Determine the conditions under which parameter values correspond to the required operating mode. For example, if the switch is on and the pressure is greater than 50, then this is the 'In operation' mode.
Algorithms for determining the operating mode are specified by the user during the initial system setup. The C# language, which allows coding algorithms of any complexity, is used to code the algorithms.
Based on the data from the operation time module, switching diagrams, operation time reports, and OEE, MTBF, MTTR indicators are built.
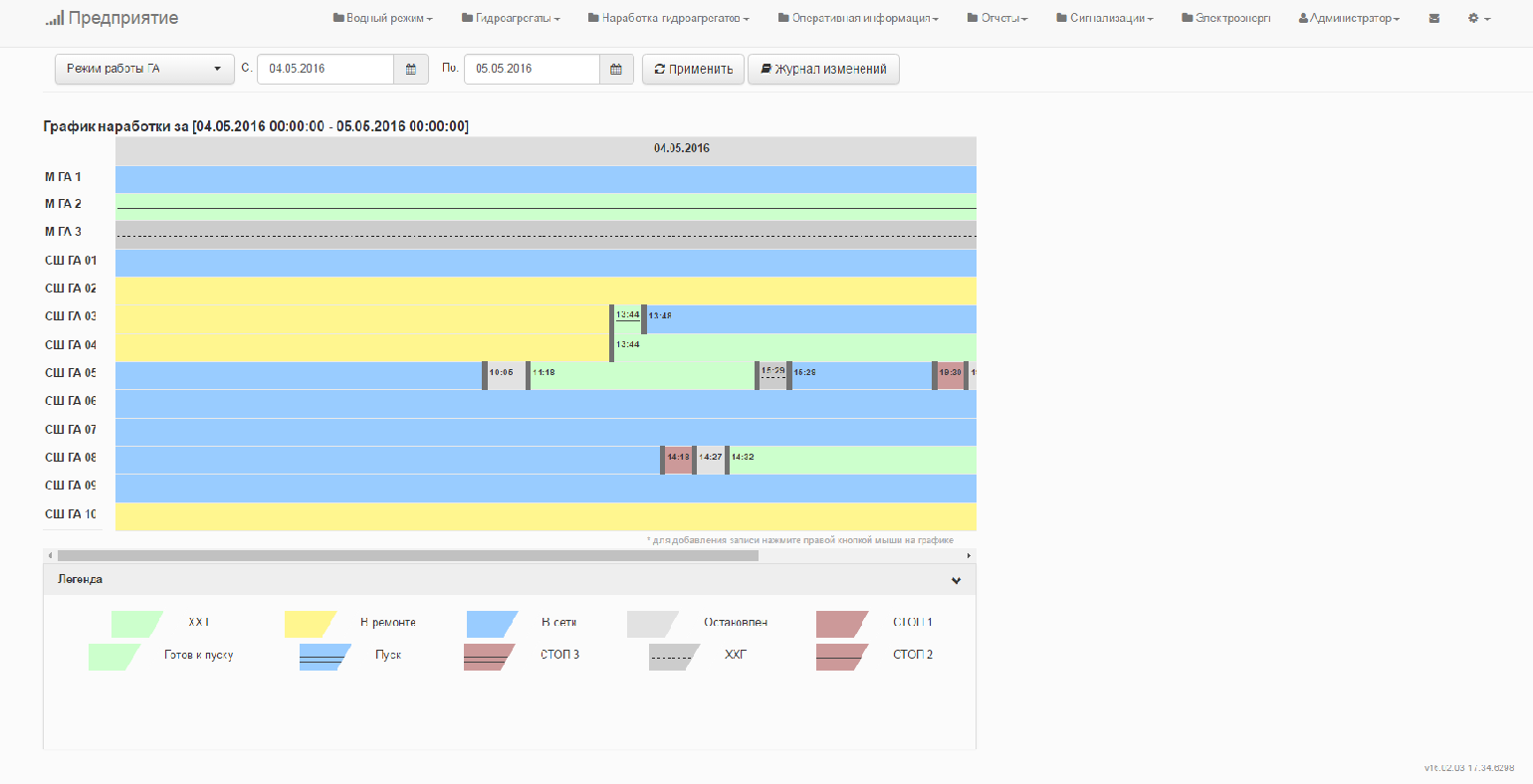
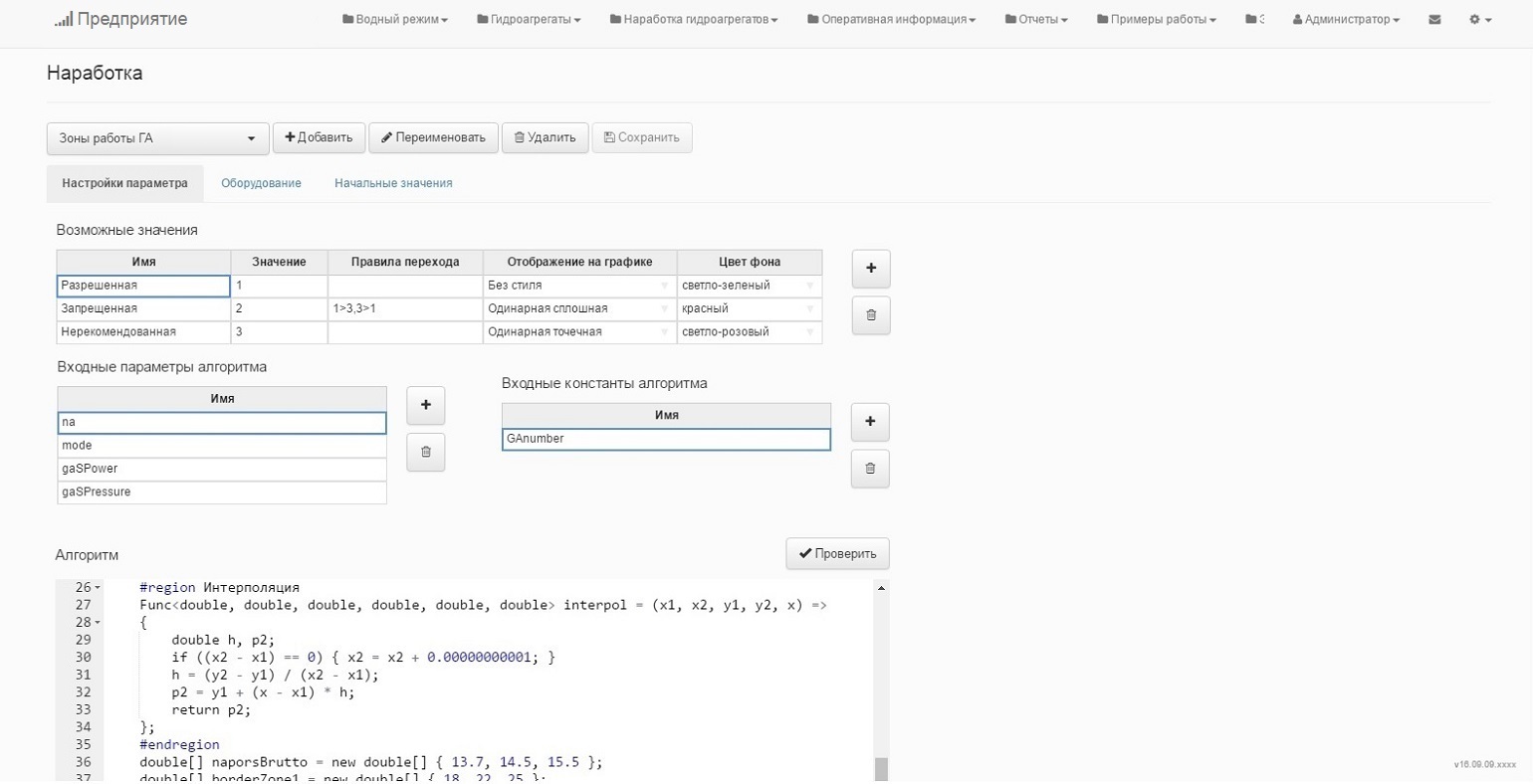
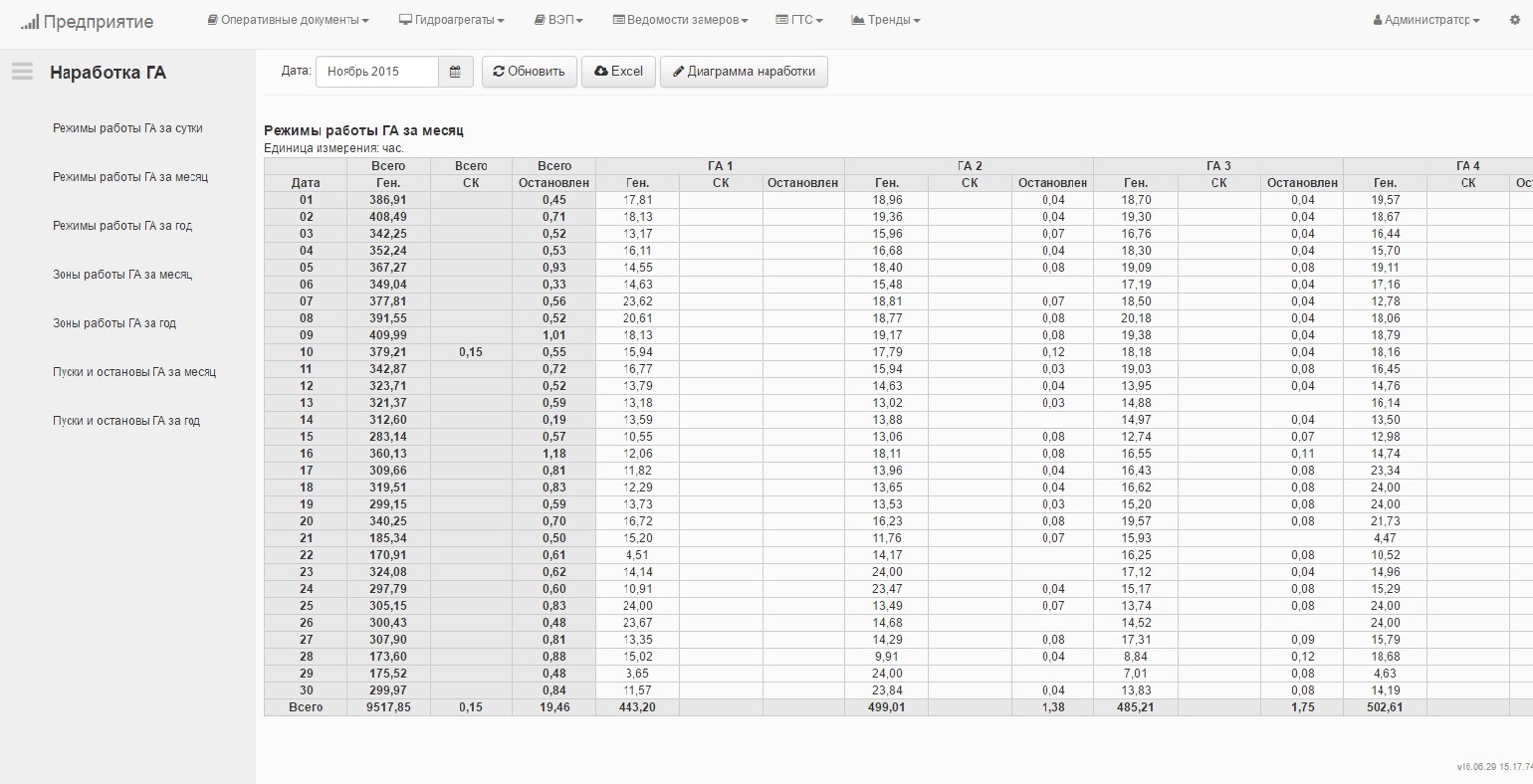
Features:
- Accounting for equipment operating time and downtime
- Accounting for the number of equipment starts and stops
- Accounting for equipment operating time in various modes
- Viewing operation time data in graphical and tabular form
- Creating and editing algorithms for calculating equipment operating modes
Switchover forms
The switchover forms module provides the enterprise's operational personnel with a means of creating and automatedly processing switchover forms. A switchover form consists of a set of operations that need to be performed on the running equipment. Operations can include both checking the equipment status and controlling the equipment.
Using the switchover form designer, the operational personnel can independently create a switchover program. If the equipment tags are set up in the SCADA system, the operations for checking and controlling can be automated. When creating a switchover form, the user can automate checks. To do this, it is enough to select the related parameters from the equipment tree.
The system provides the following capabilities:
- Import existing standard switchover forms.
- Create and edit new switchover form templates.
- Automate checking the conditions for readiness to execute the switchover form.
- Automate the execution of switchover form operations.
- Maintain a directory of standard operations.
- Work with alarms and warnings.
- Work with remote control keys (for HPPs).
- Execute the switchover form in player mode.
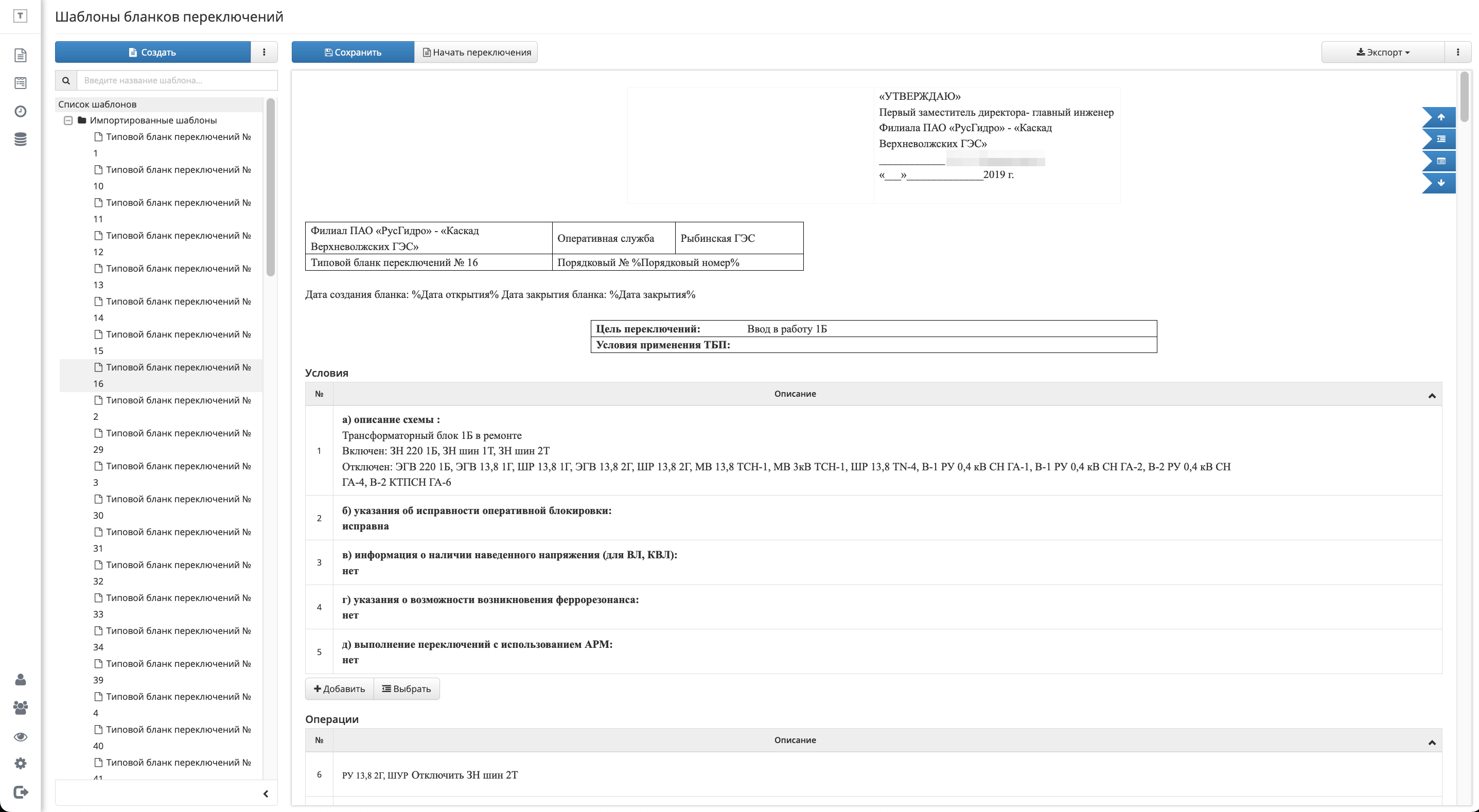
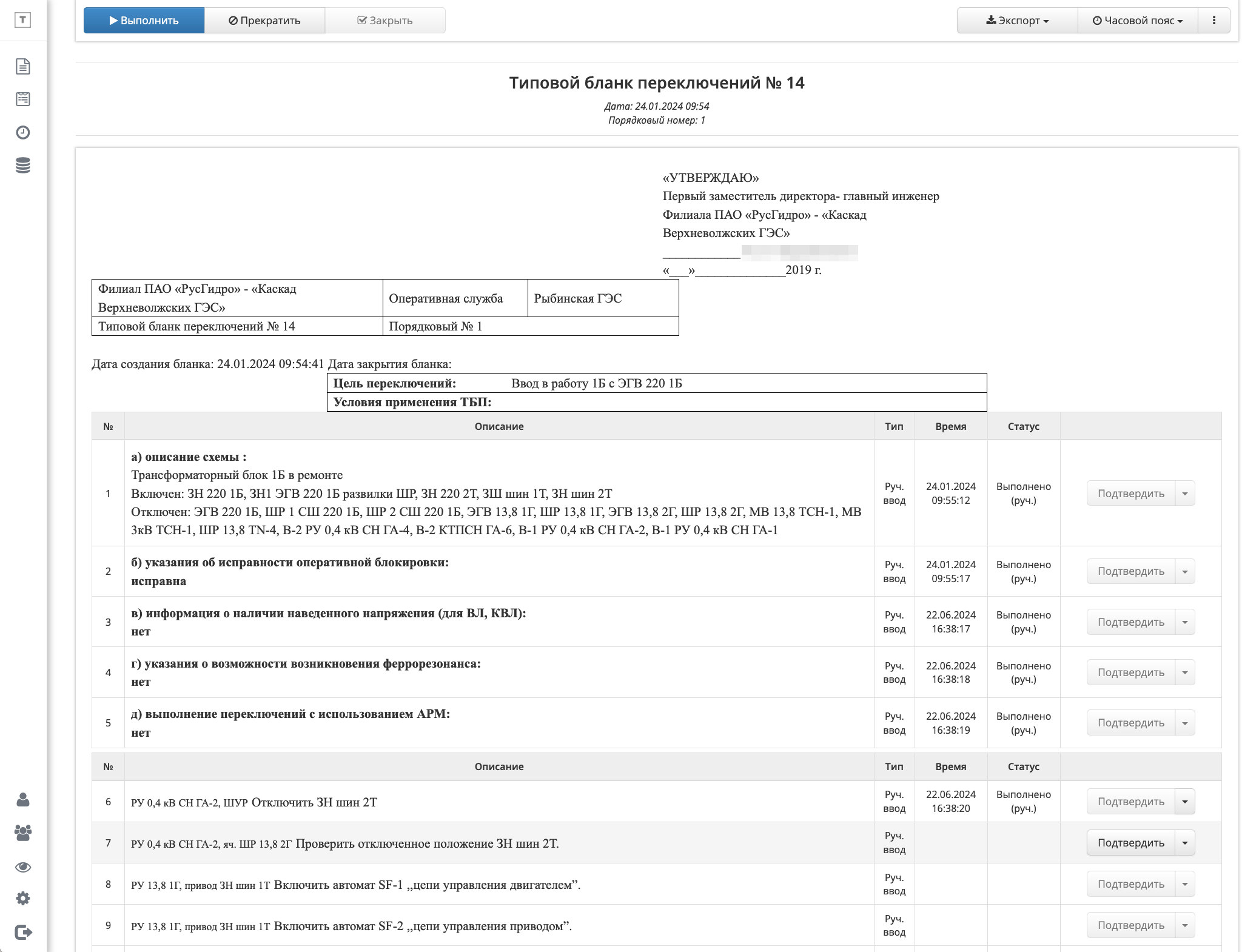
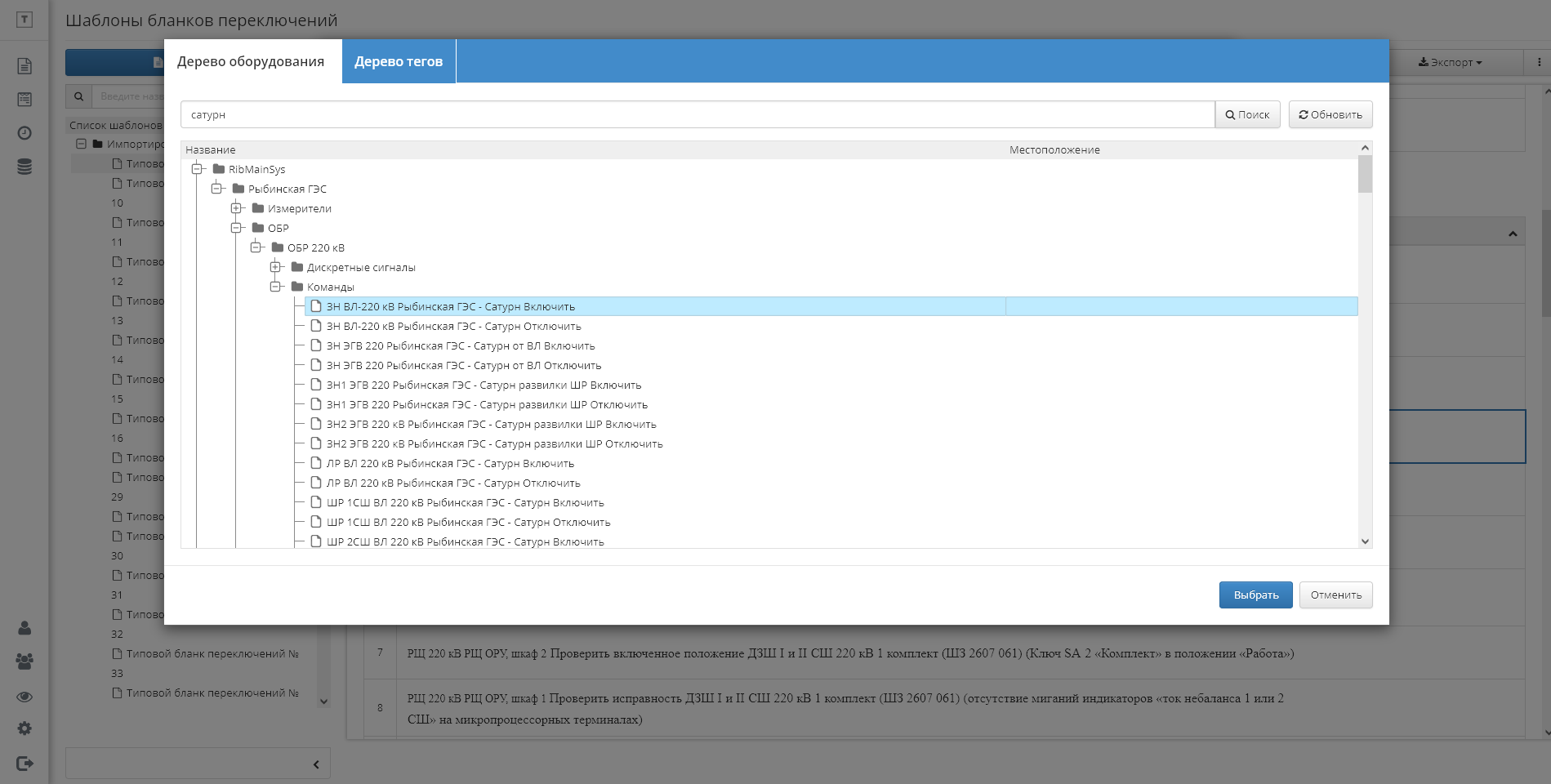
Material balance (prototype)
The task of calculating the material balance is an important part of production accounting for every oil refining enterprise. The material balance calculation subsystem allows automating the following processes:
- Create and maintain a model of the enterprise's material flows.
- Prepare data for the calculation, identifying measurement errors and determining the imbalance composition for each production object.
- Calculate the material balance of production operations, resulting in a set of reconciled and reliable data on the stocks, movement/transformation of raw materials and petroleum products necessary for production analysis.
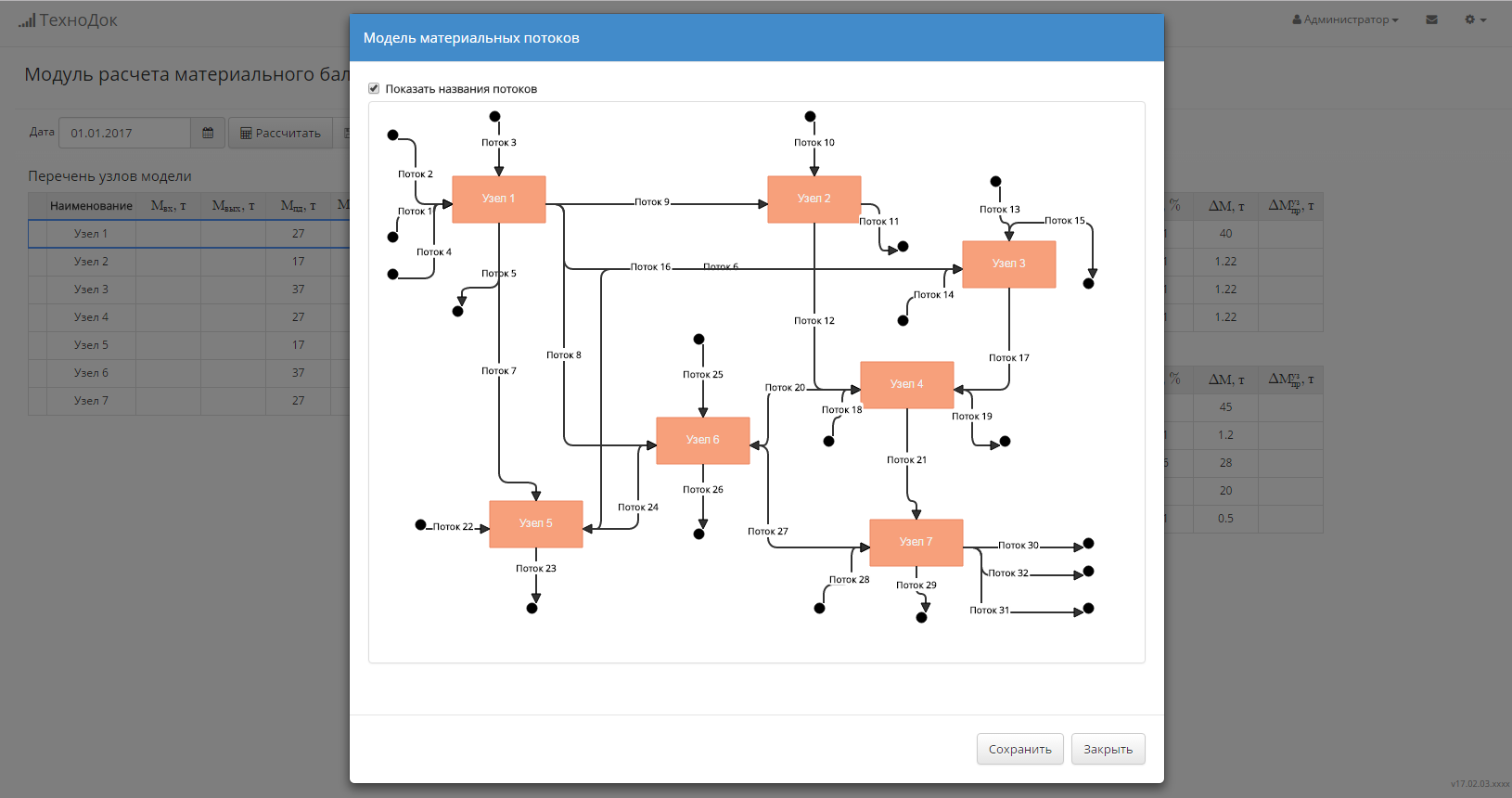
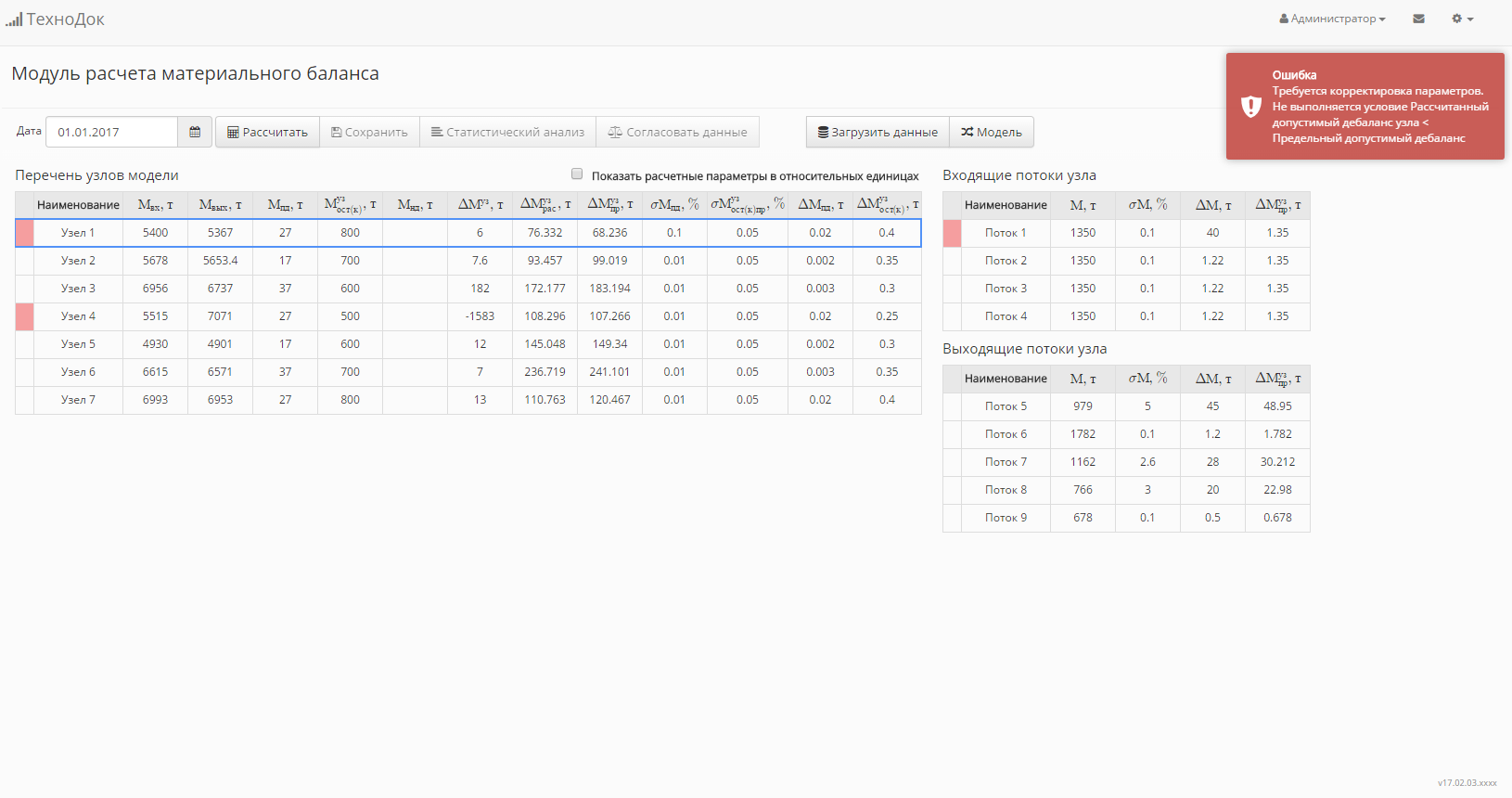
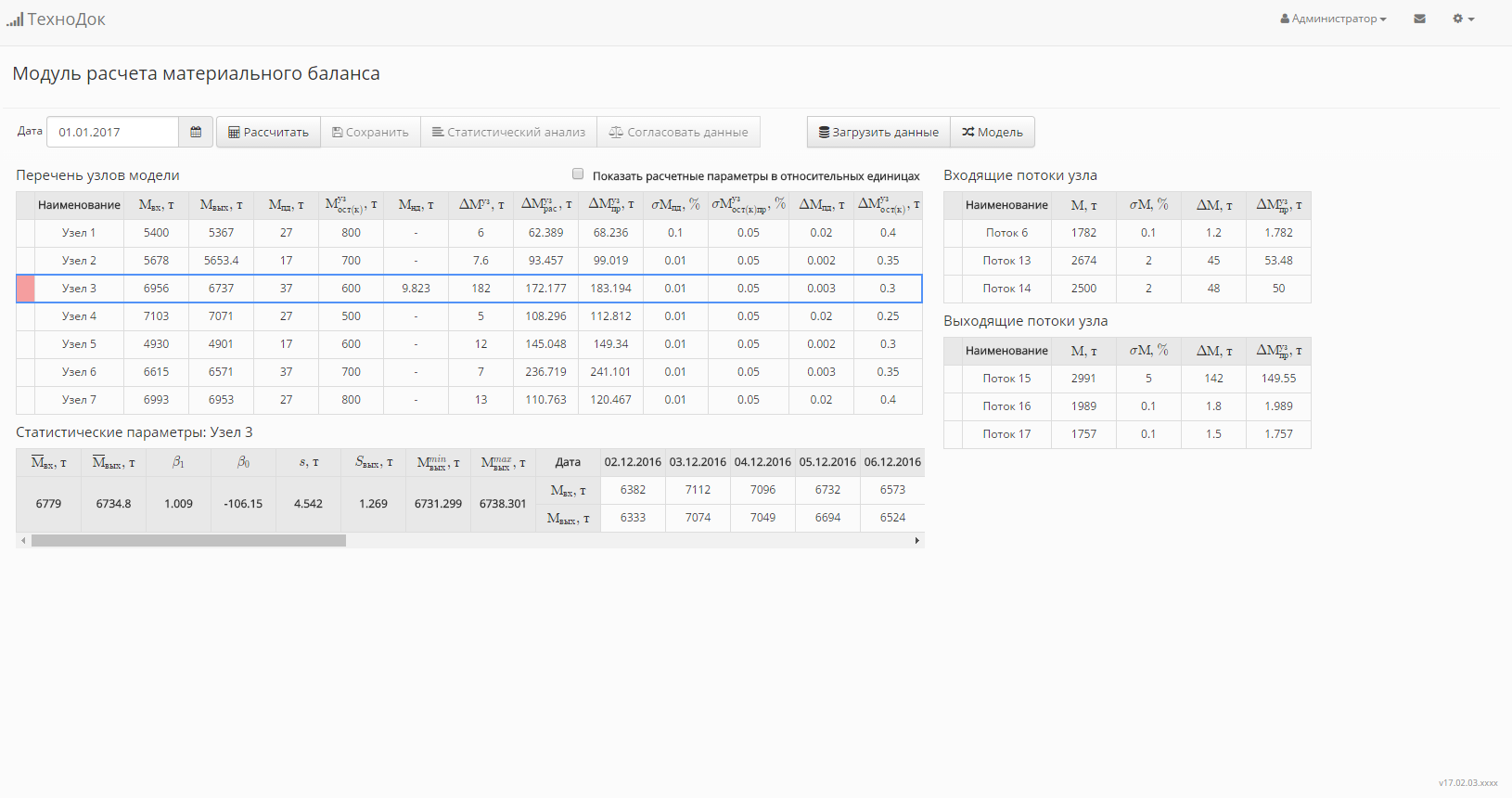
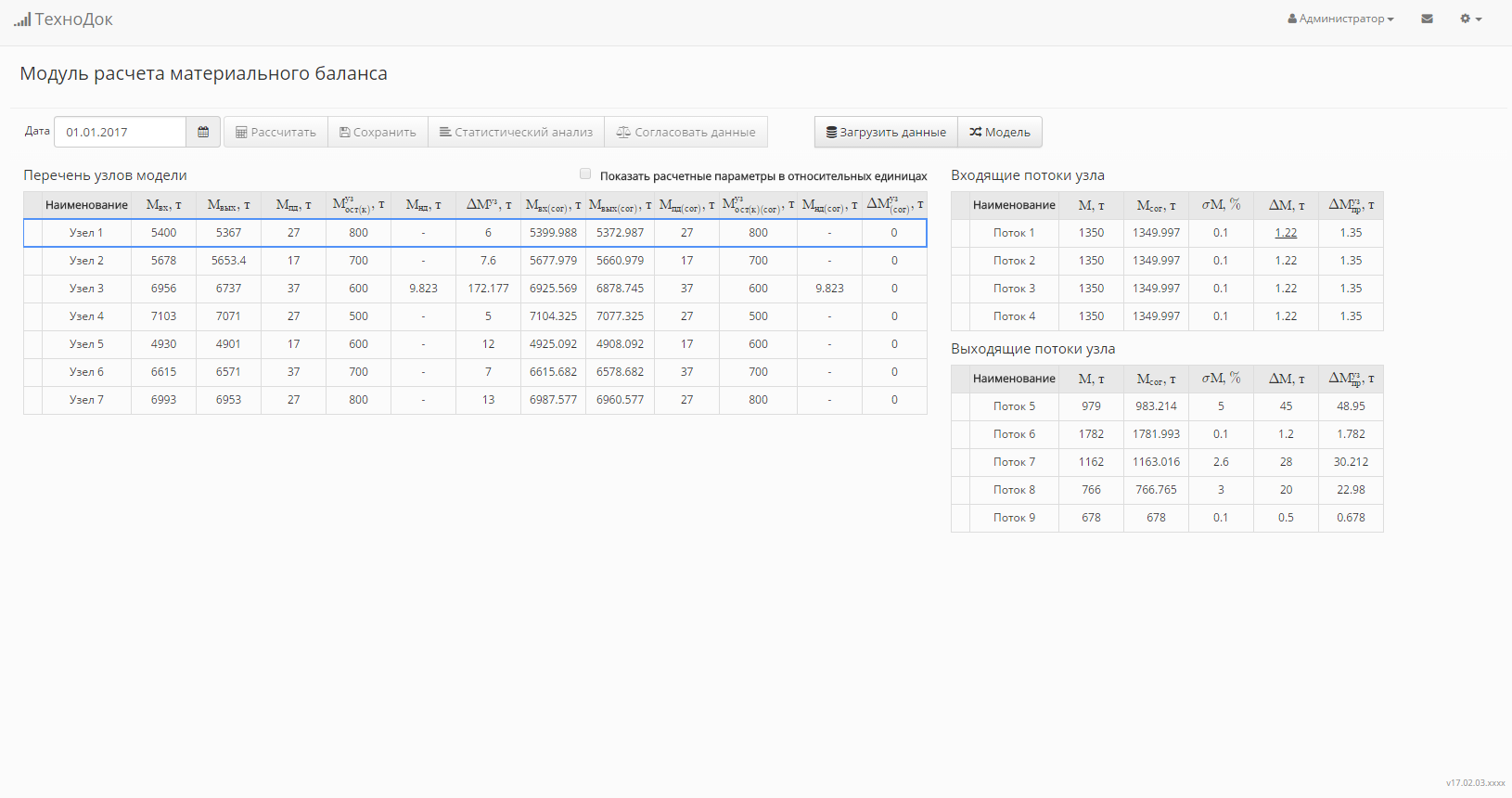
Preparing Data for Material Balance Calculation
To ensure the reliability of the material balance calculation, the system analyzes primary data, identifies places and causes of gross errors in measurement results.
The following methods for identifying gross errors are implemented:
- analyze the impact of current production modes on the reliability of measurement results;
- analyze the imbalance magnitude at each node based on statistical data analysis.
The subsystem provides the ability to make adjustments based on the analysis results. After eliminating all possible gross errors, the composition of the imbalance for each balancing node is determined.
Calculating the Material Balance of Production Operations
As a result of the data preparation process, a set of data free from gross errors but not reconciled among themselves and recording the execution of production operations within the boundaries of balance objects is formed. The data is not balanced between the inputs and outputs of objects and the operations of movement between objects are not reconciled.
The material balance calculation subsystem allows for the reconciliation of data and the calculation of the balance of production operations.
The data reconciliation process across the entire enterprise distribution network is performed automatically using the least squares method. The result of the reconciliation is the finding of minimal corrections to the measurement results of material flow masses that satisfy certain technological relationships and ensure compliance with the law of conservation of mass.
Demonstration
Below is an example of working with the material balance calculation subsystem. It covers scenarios for data preparation for the calculation, identification of gross errors, reconciliation, and calculation of the production operations balance for the day.
Enterprise model description
An object-oriented approach based on the Common Information Model (CIM) methodology is used to describe reference information. The methodology is based on the principle that any set of objects in an enterprise can be described using classes, relationships, and attributes. This assumption allows describing the hierarchy of equipment and parameters in the form of a dependency graph and viewing directories in the required hierarchy.
Reference information can be used in the report designer. For example, a report parameter can refer to a list of equipment, datapoint values, calibration dates, etc.
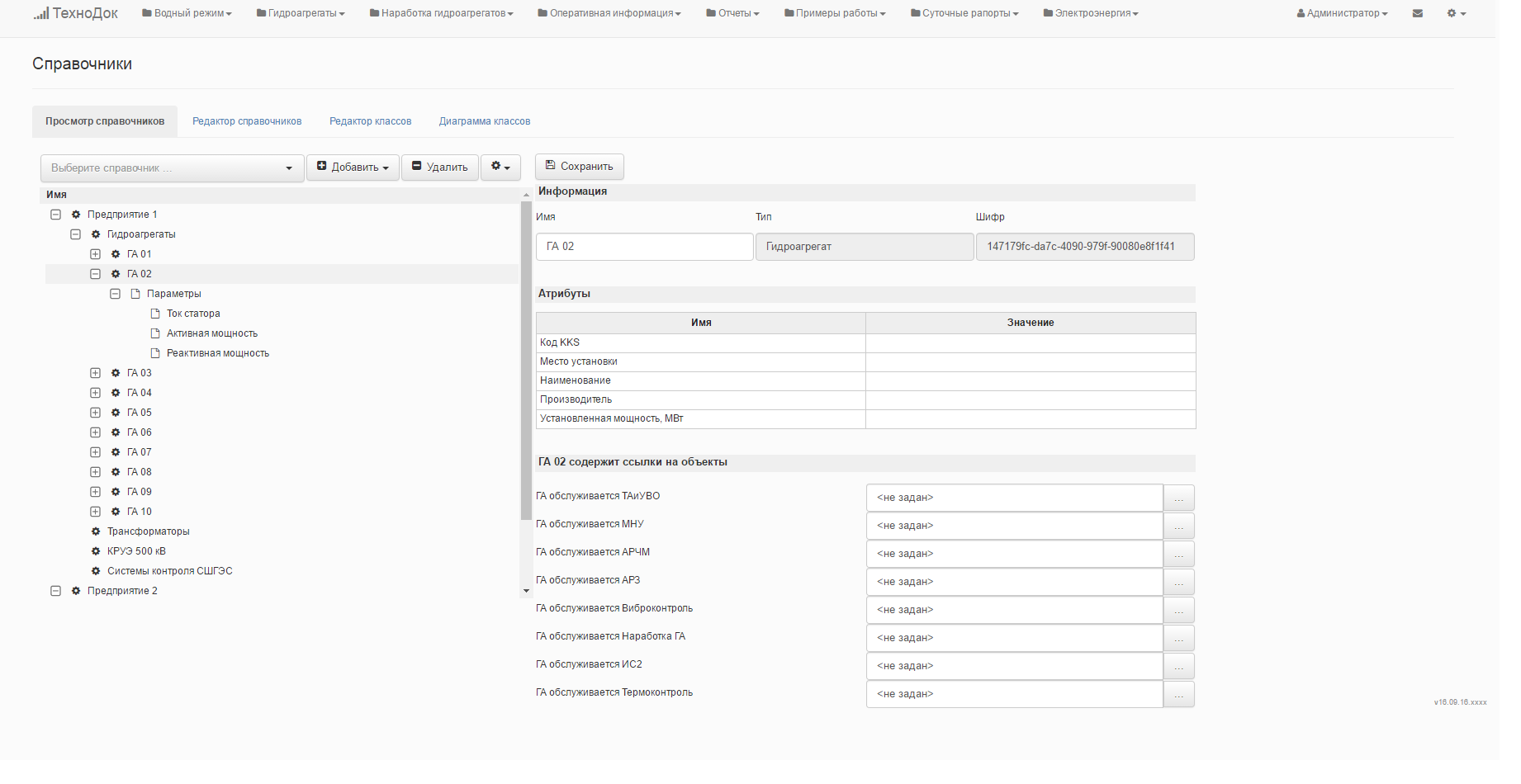
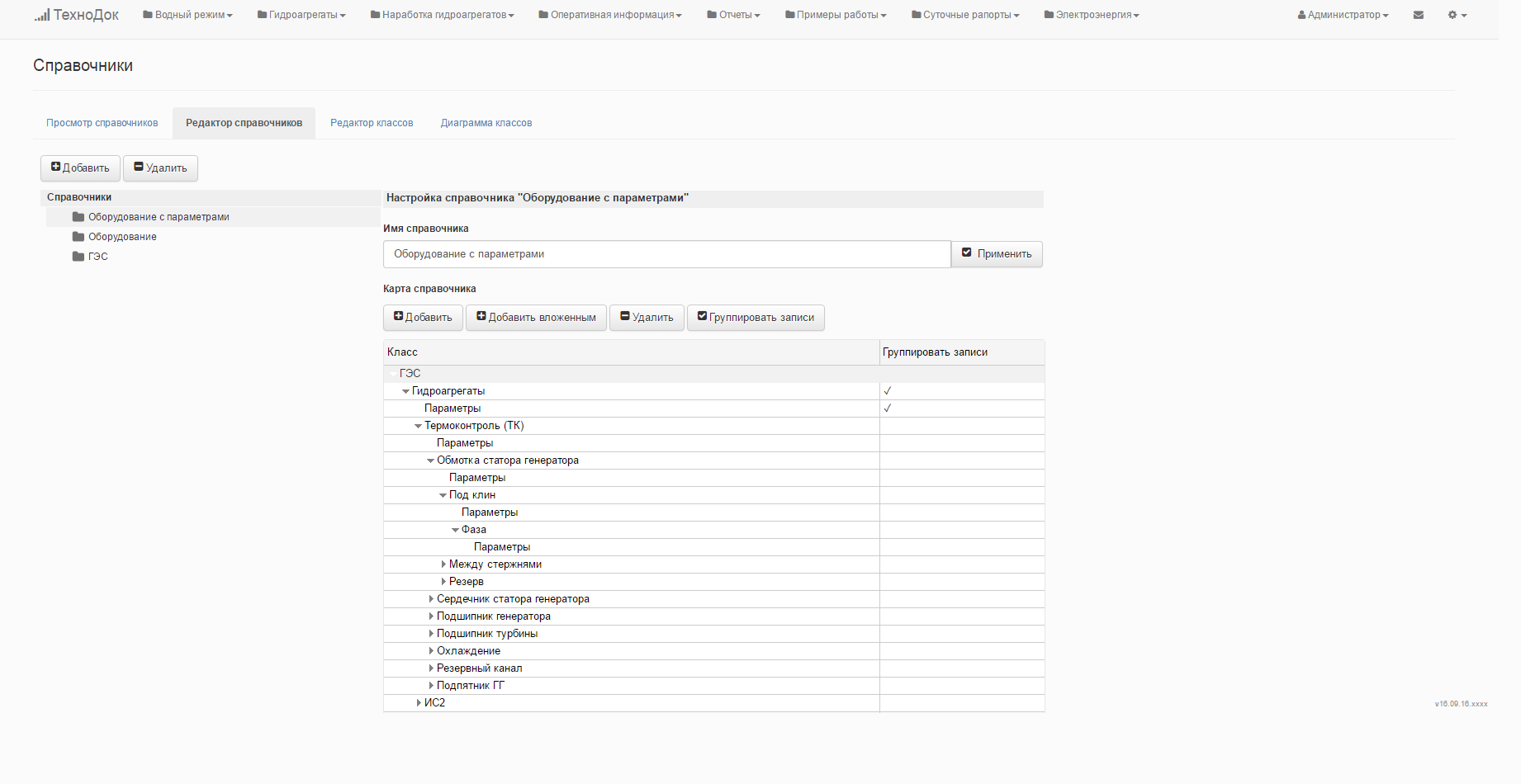
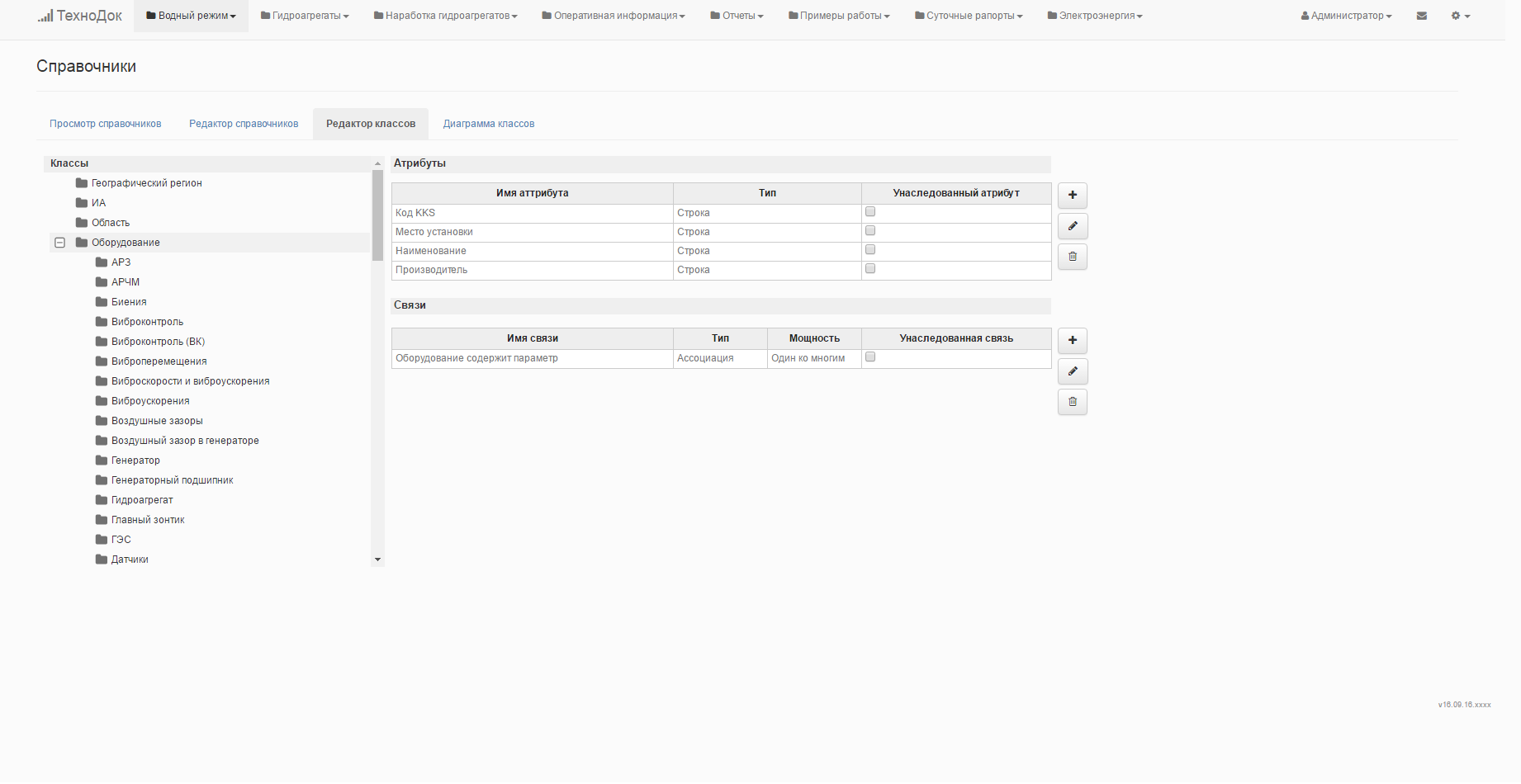
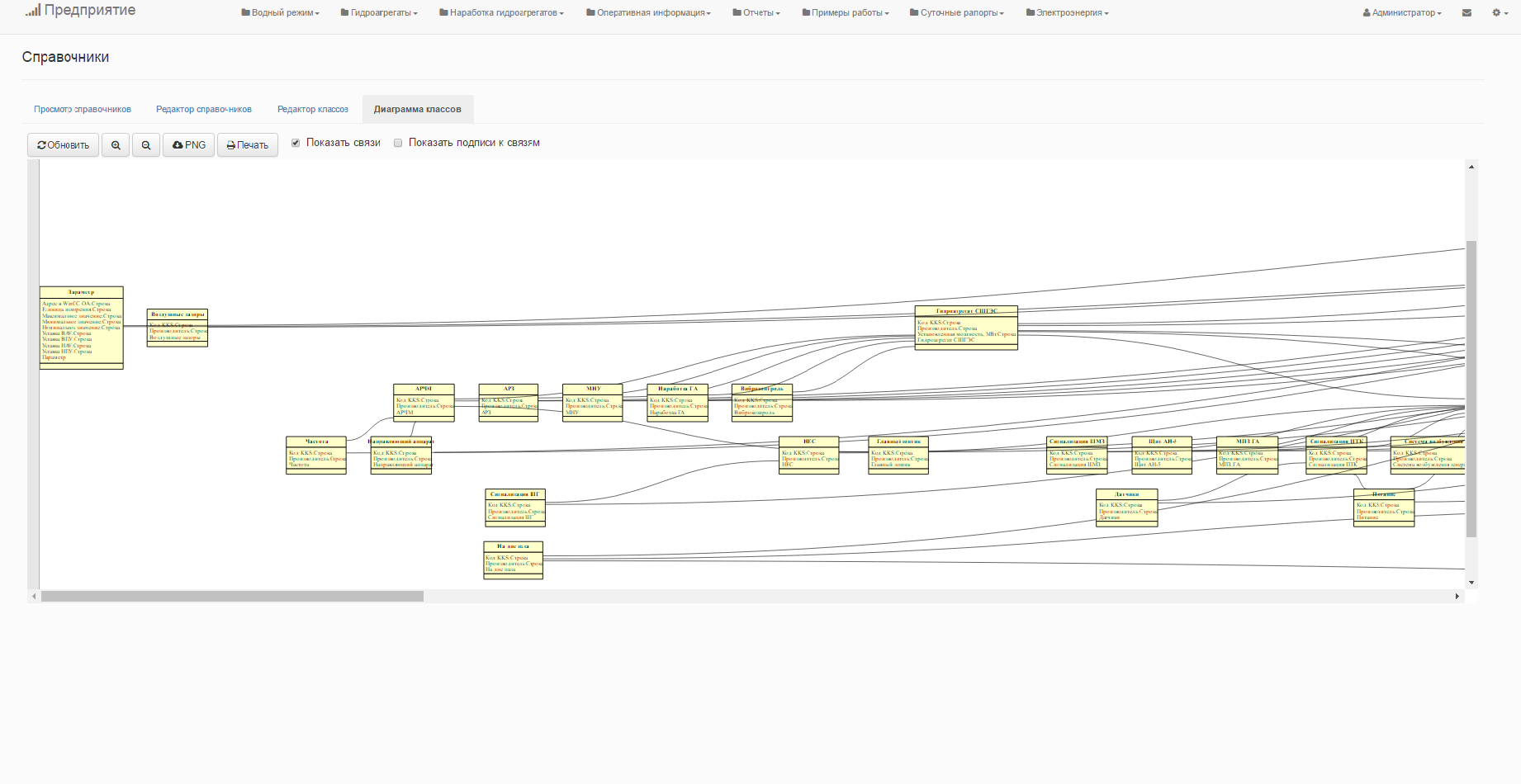
Integration options
Drivers have been developed to interact with enterprise systems, allowing data to be obtained via industrial protocols, from databases, text files, and information systems via provided APIs.
List of drivers:
- OPC UA
- OPC DA/HDA
- PostgreSQL / Oracle / SQL Server
- ODBC
- Alpha.Platform
- КАСКАД Цифра
- WinCC, WinCC OA
- Excel
- Manual Input
- ASUREO
- Pyramid 2000 PC
TechnoDoc provides tools for developing your own driver in C#. Therefore, if there is a need to collect data from a new system, a driver can be developed either by our specialists or by the customer's technical specialists.
Deployment options
TechnoDoc can be installed as standalone software or as part of a SCADA system. For storing service data, TechnoDoc can use one of the following DBMS: PostgreSQL, SQLite, MariaDB, MS SQL Server.
The client application is a thin client developed using HTML5 and JavaScript technologies. This solution allows working with the system on computers and mobile devices where there is a browser.
The client application can be integrated into WinCC OA project as a web component with SSO authentication.
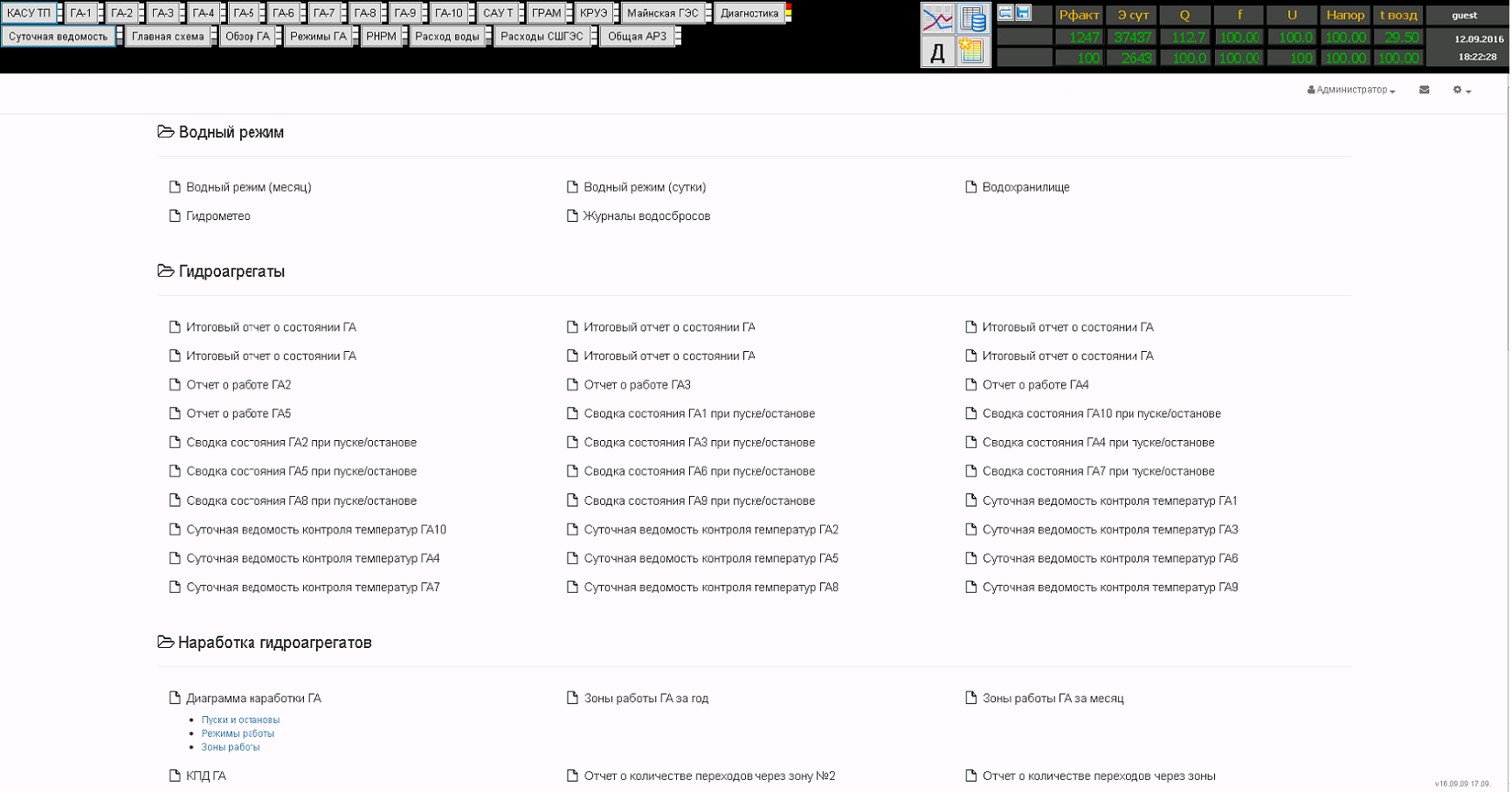